Engineered to Defy Gravity
THE SELF-BALANCING CUBE is purpose-built to balance on a single edge, integrating mechanical, electrical, and software systems into a compact and visually striking design. Designed and developed by a team of five students, this project embodies the fusion of mechanical engineering, electronics, and computer science.
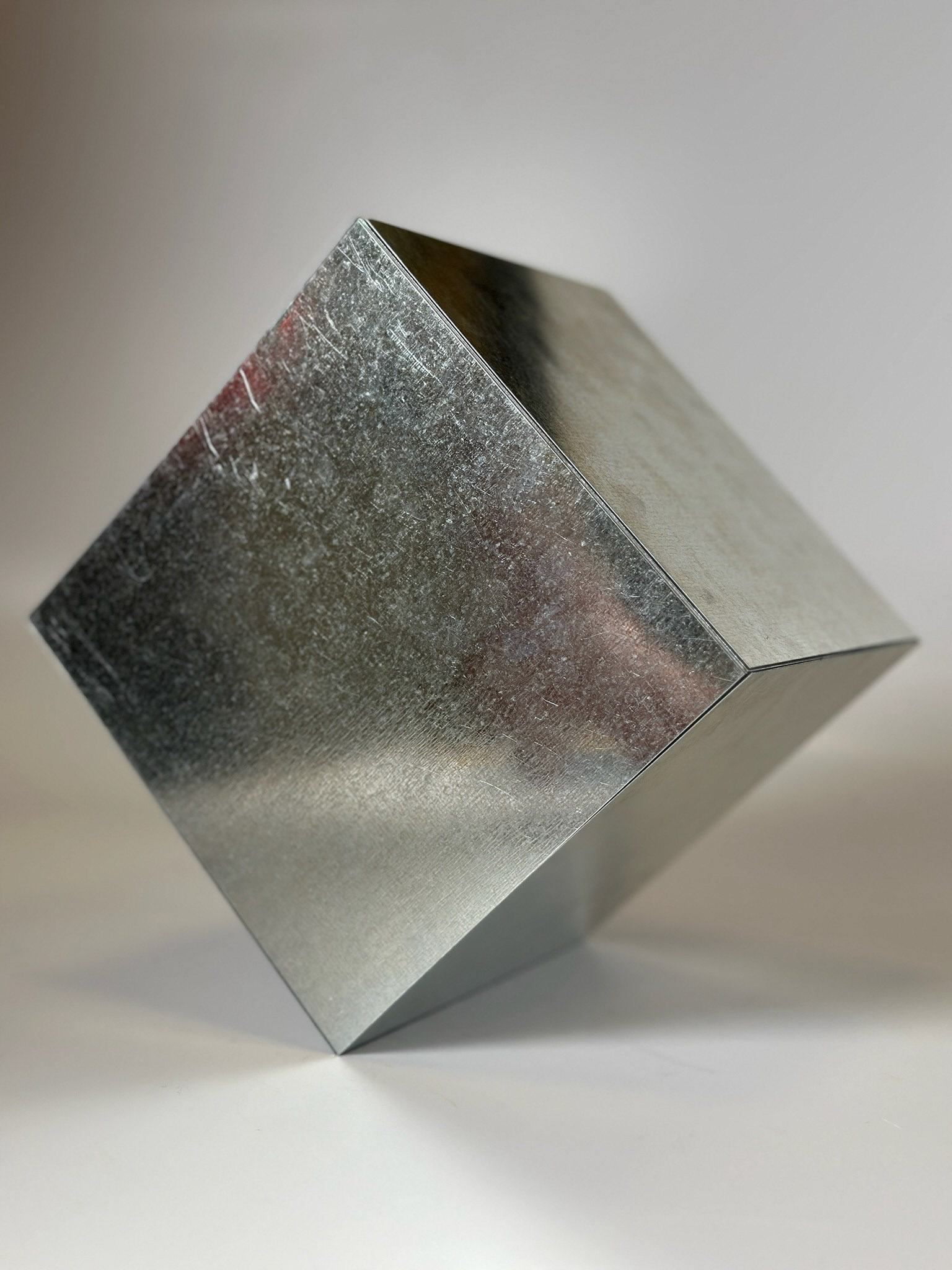
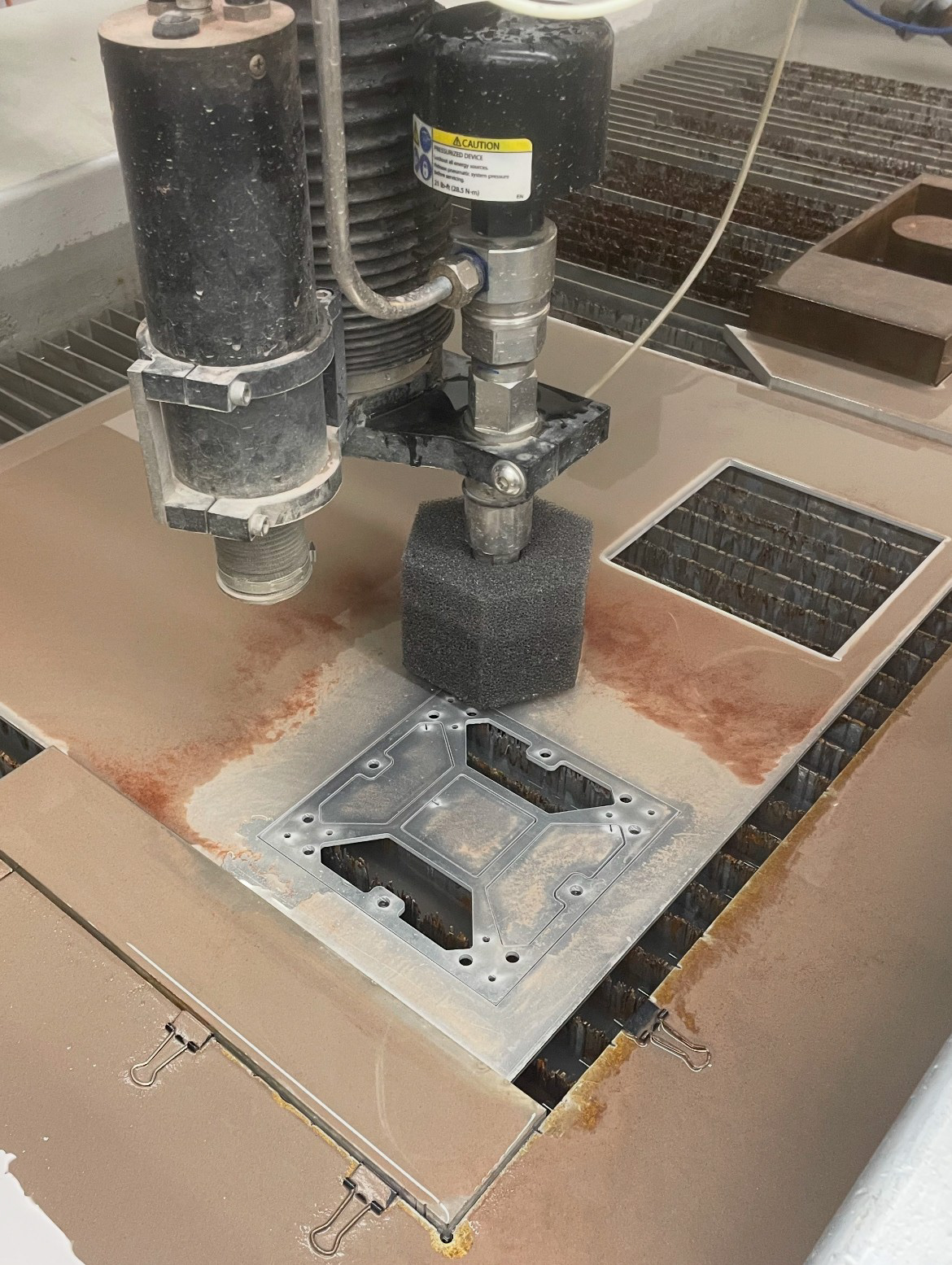
Precision Machined and Optimized for Manufacturing
Designed using FEA and topology studies, 0.125" 6061 aluminum plates are light-weighted using the waterjet. Utilizing pre-existing holes from water-jetting the light weighted plates are mounted to the mill to create miter joints.
Water-jetted 1018 steel flywheels maximize moment of inertia, utilizing high-density material for space-saving performance.
Brass motor standoffs are lathed for durability and precision.
Optimized and Intentional Design
Mitered aluminum plates are joined using custom 3D-printed brackets for a seamless fit and ease of assembly.
Magnetic mounting using press-fit stubs enable interchangeable sideplates without compromising functionality
3D-printed mounting for optimal IMU and electronics placement.
Final electronics integrated on a perfboard facilitating robust and clean harnessing.
Every detail, from countersunk holes for a flush finish to the optimized plate light weighting, reflects a commitment to form and function.
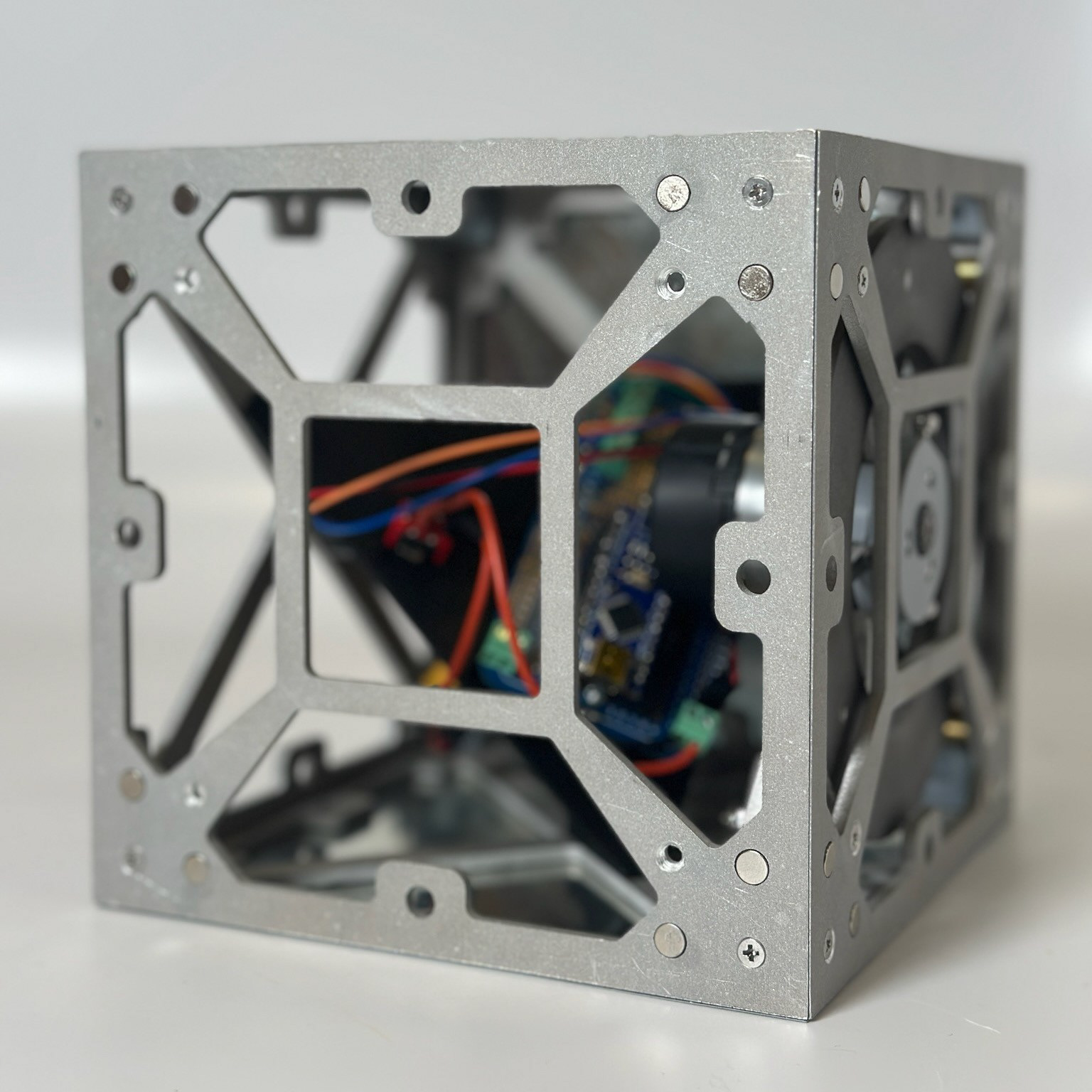
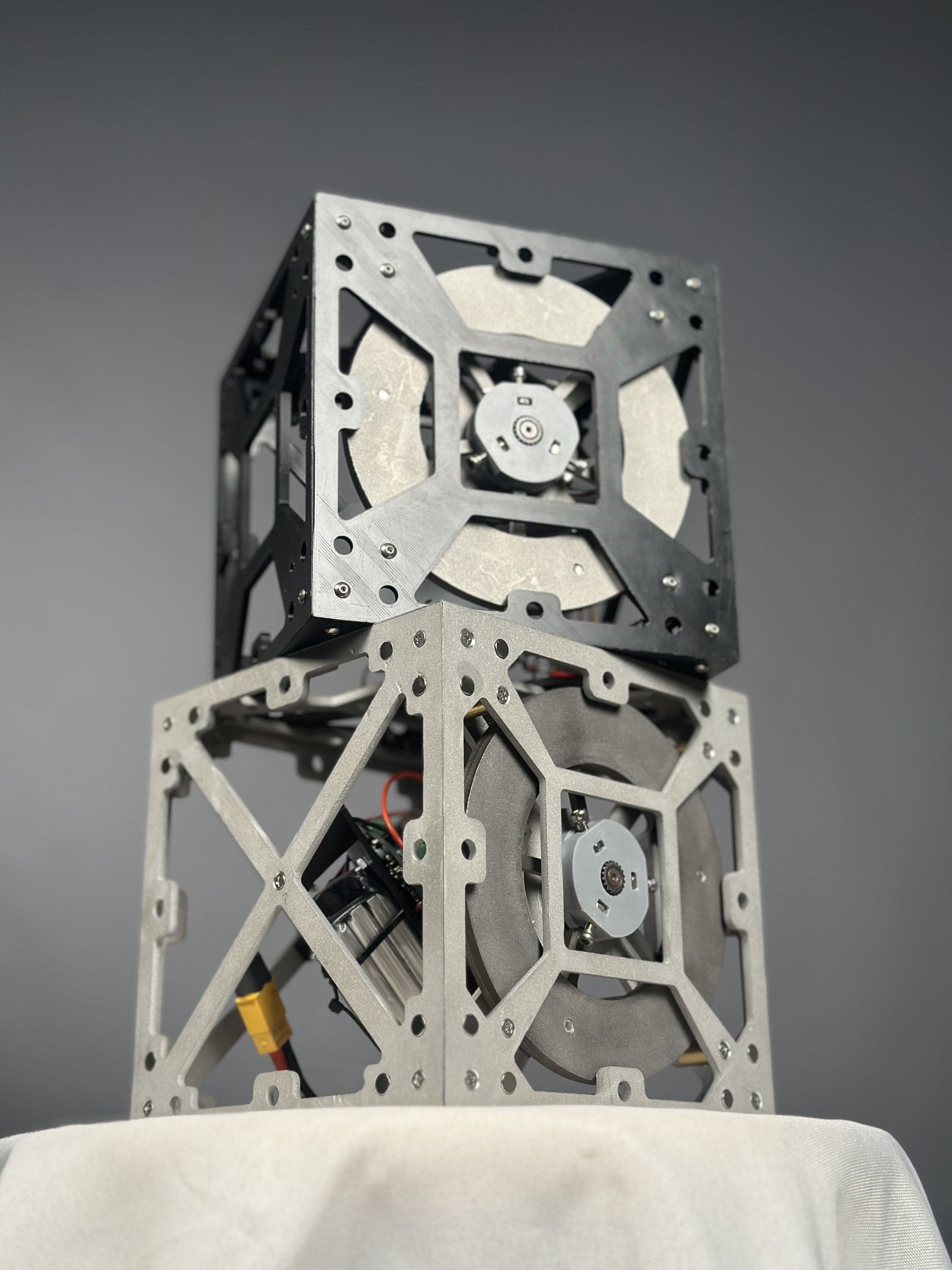
DESIGNED FOR RAPID TESTING AND MODULAR
Designed to be both 3D printed and machined. Allowing rapid versatile testing and tuning.
Extra motor mounting holes added to support potential enhancements, including balancing on a vertex.
CAD
Designed in SOLIDWORKS, using SOLIDWORKS Simulation for FEA analysis of side plates and light-weighting.
Used public drive based file sharing system for collaboration with teammates.
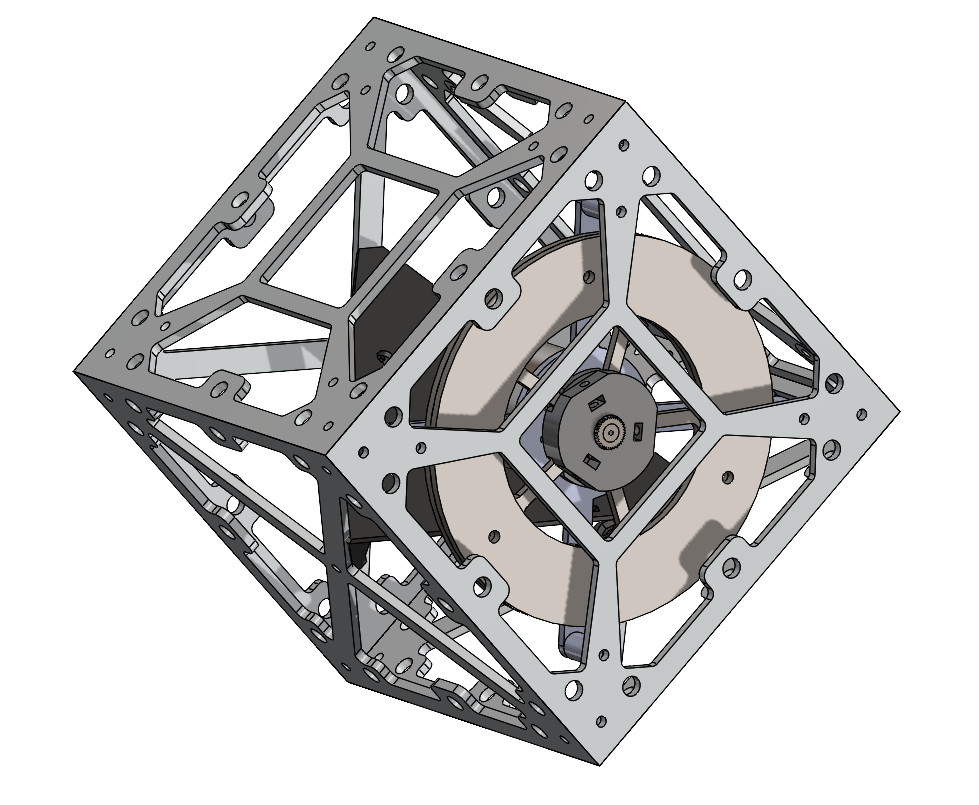
Self-Balancing Cube in Action!